
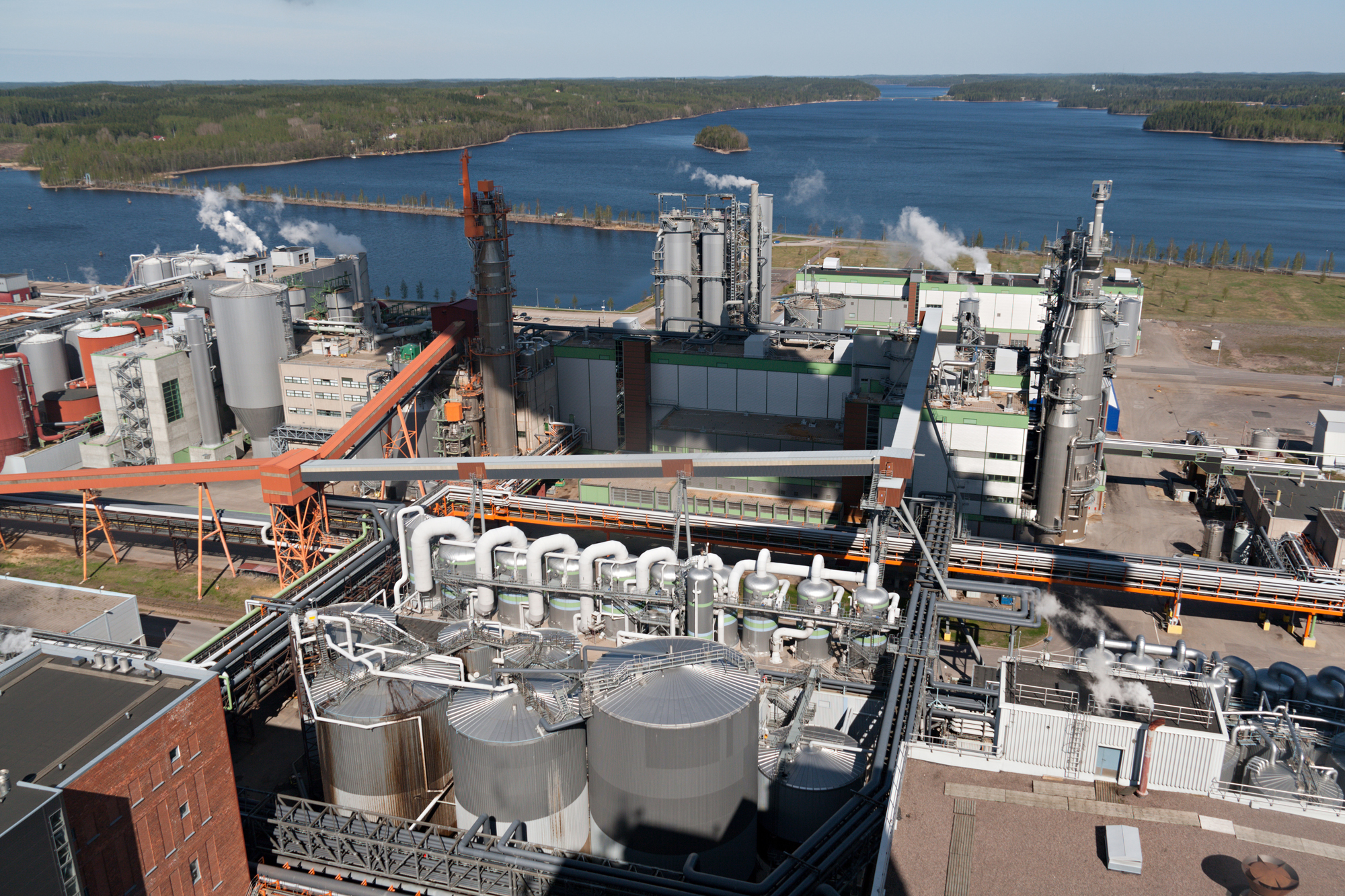
Supply Chain Project at a Paper Mill
Following a period of rapid organizational change, this team focused on cost, inventory and product damage
“I am proud to say that the linkages between the strategic direction at the executive level and its translation throughout the Supply Chain Group, is more fully understood today than at any point in my 26-year history with the company. People now have a much better sense of how their work impacts the bottom line. For me as a director, this process has allowed me to confidently step back from the day-to-day, empowering my managers and their direct reports to do what they must to achieve the targets we have set together.”
—Director, Order Fulfillment
Context/Challenge
This Supply Chain continuous improvement project started during a period of rapid change – during the RLG project, the ownership of the company changed twice, the previously separated paper and pulp divisions were reintegrated, and the company successfully merged with an equal sized competitor.
The focus remained on cost rationalization through supply chain, inventory management and minimizing product damage.
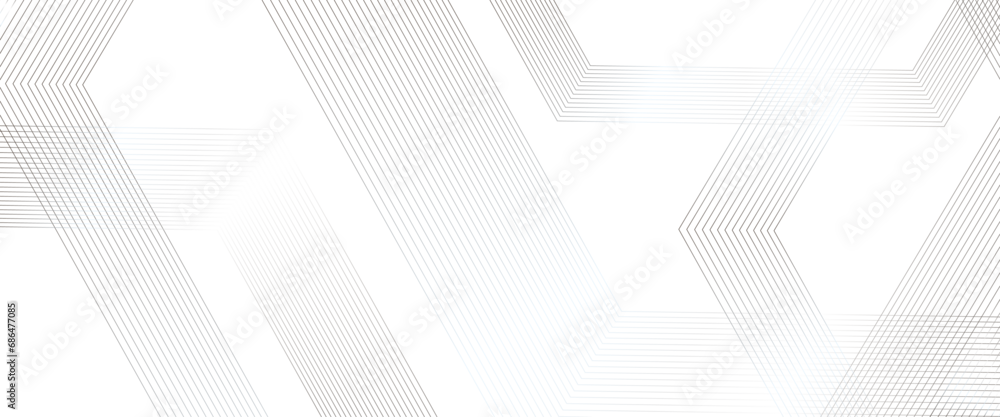
Approach
Beginning with a discovery phase, the RLG team and client leaders examined the drivers, opportunities and key resistant points – which revealed communication, process and decision-making gaps across the organization, plus little visibility beyond the senior leadership team to the ambitious cost goals that were sought.
- Mission statements and key success criteria for the initiative were established around a centrally organized program. These were widely communicated through a deliberate strategy.
- Operating Rhythm™ scorecards were introduced to all teams to identify performance gaps, with a monthly cycle of accountability business reviews to review and collaborate on forward actions.
- Continuous improvement participation was asked of all employees, with a quarterly “stop, assess and get feedback” milestone system.
- All crew, trades and management meetings, communication processes and interactions were reviewed, and a new Operating Rhythm introduced to leverage strengths and correct gaps.
Result
Notwithstanding this turbulent environment, the Supply Chain team successfully improved the key business processes, adopting a continuous improvement culture with accompanying tools, processes and changes in leadership styles which led to cost reductions of $33 per tonne.
- Project results achieved a total financial benefit for the client of $36 million.
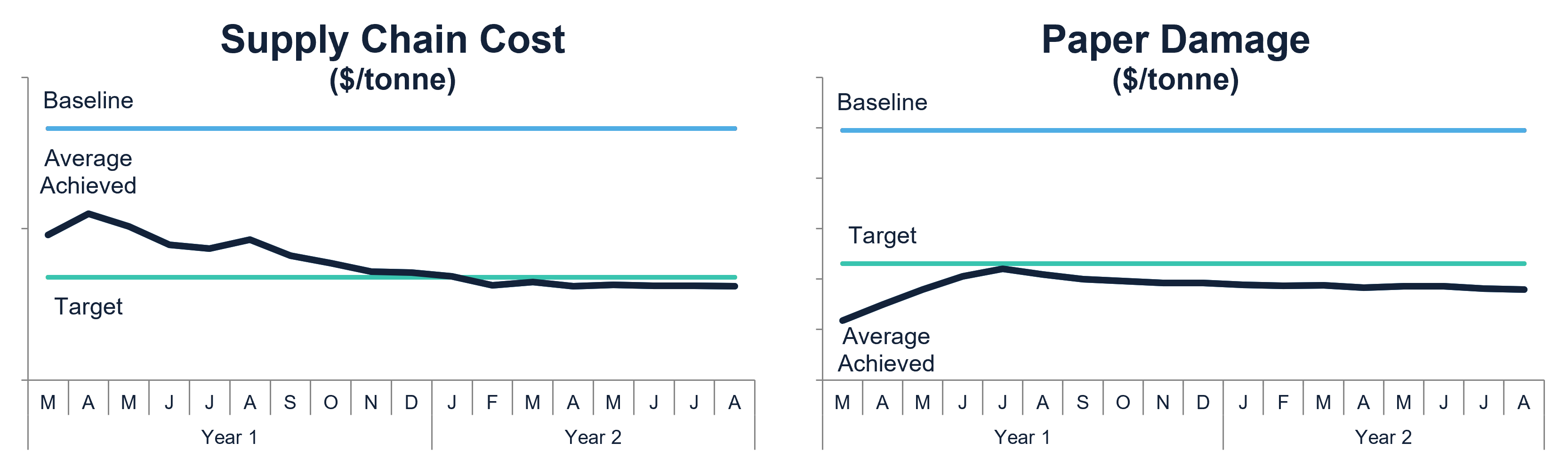
Ready to change the way YOUR business is done?
We would love to learn about your unique challenges. Contact our team for a no-obligations conversation or even a site visit.
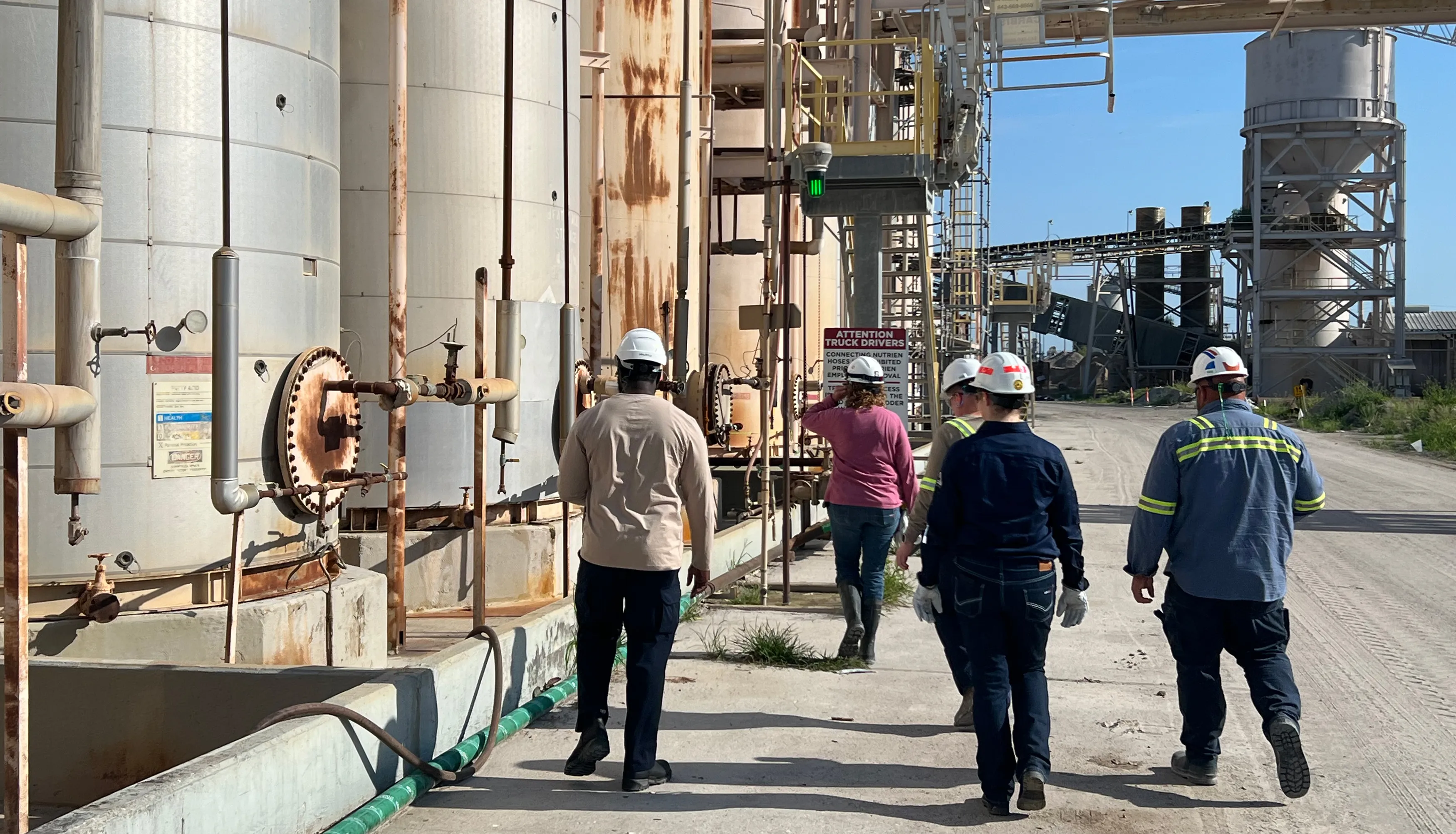