
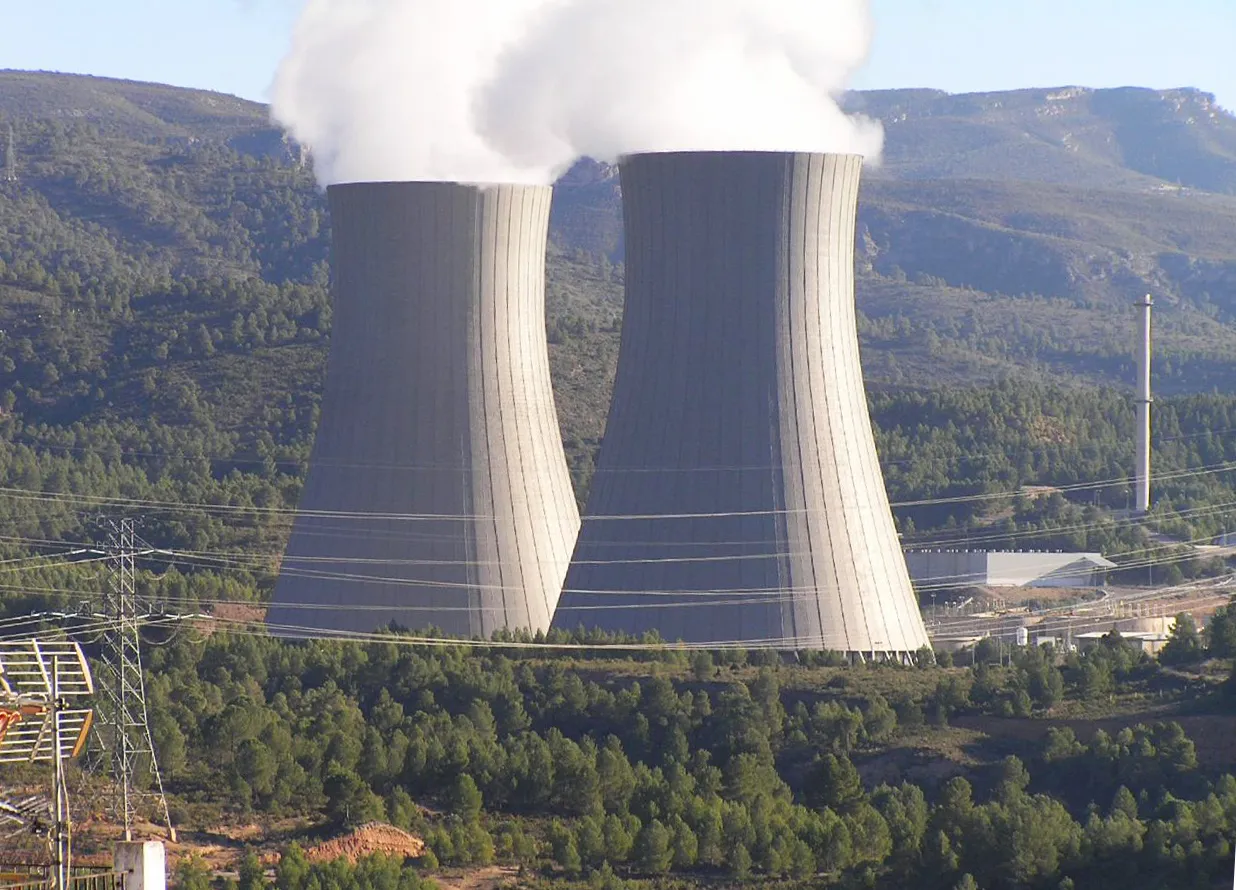
Nuclear Power Plant Targets Maintenance Performance
This nuclear operator needed to boost their operational performance with stronger processes, improved front-line ownership behaviors, and a renewed sense of vision and purpose. A key focus was their core maintenance workflow.
“It’s about working with the front-line managers and section managers to raise their cost awareness, manage together as one site, focus on their leadership and management behaviours and not doing things the old way.”
— Vice President Maintenance
“… within my Maintenance Department we have increased our productivity by 100% over the last two years, increased our output by 90%, and increased the quality of our planning by 50%. More importantly, through the coaching assistance of RLG, our section managers and first line managers have developed a business understanding that did not exist before.”
— Maintenance Manager
Context/Challenge
This large nuclear plant with 8 reactors and 3700 highly skilled men and women needed a shift in culture following an ownership change. After a lengthy search, they chose to partner with RLG in the challenge of creating critical front-line engagement and establishing a culture that targeted outstanding performance.
- Cost Pressures: Operating costs for labor and contractors were considerably higher than targets and competitors
- Broken Promises: Maintenance outages routinely went longer than promised, with significant commercial consequences
- Culture was Bitter: Morale was low and the new owner saw an opportunity to revitalize and excite the workforce
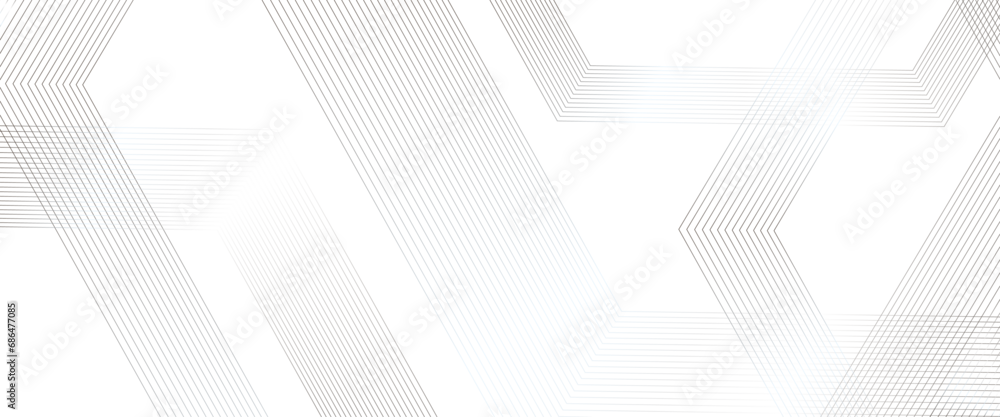
Approach
They began their partnership with RLG with the goal of bringing commercial focus to the front line to generate clear, measurable results.
- Focus and Alignment: Aligned metrics, scorecards, story boards and accountability reviews strengthened use of data, decision making, ownership and positive recognition.
- Opportunity / Risk logs enhanced the ability of the front-line managers to think about their roles as business leaders rather than technical trouble shooters and engaged crews in identifying actions to improve performance.
- RLG’s Coaching for Results methodology engaged leaders in a systematic and rigorous approach to address behaviors that limited successful execution.
Result
Over $96 million in bottom line improvements, representing an ROI of 8:1 over a 4 year RLG engagement
- More than 1 million hours of productivity gain in maintenance worth $58 million
- $18 million in capital project schedule and cost gains
- $20 million in supply chain savings, working with suppliers, vendors, logistics and contractors
- The World Association of Nuclear Operators identified three client-RLG tools as strengths for implementation in all nuclear plants worldwide
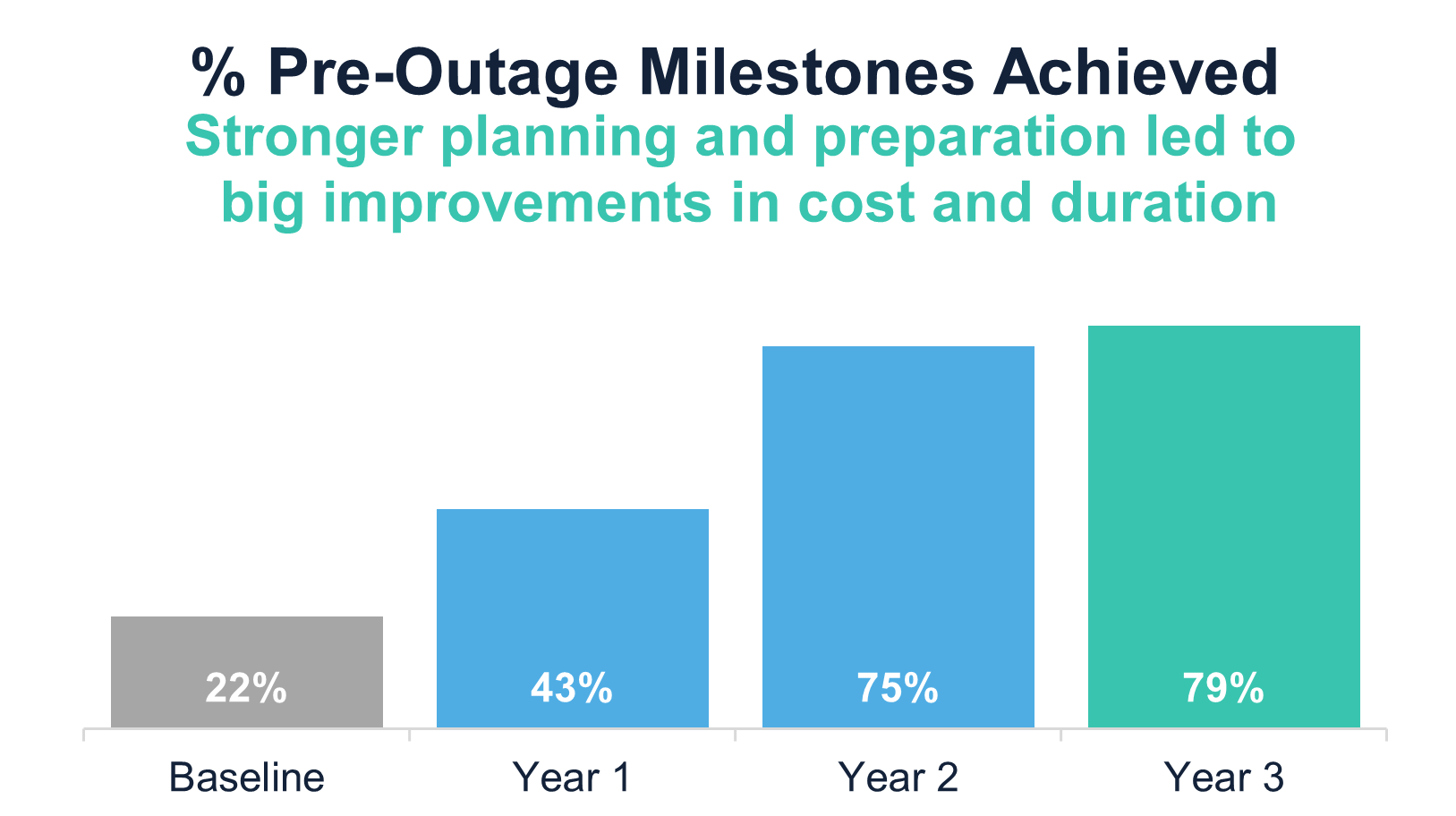
Ready to change the way YOUR business is done?
We would love to learn about your unique challenges. Contact our team for a no-obligations conversation or even a site visit.
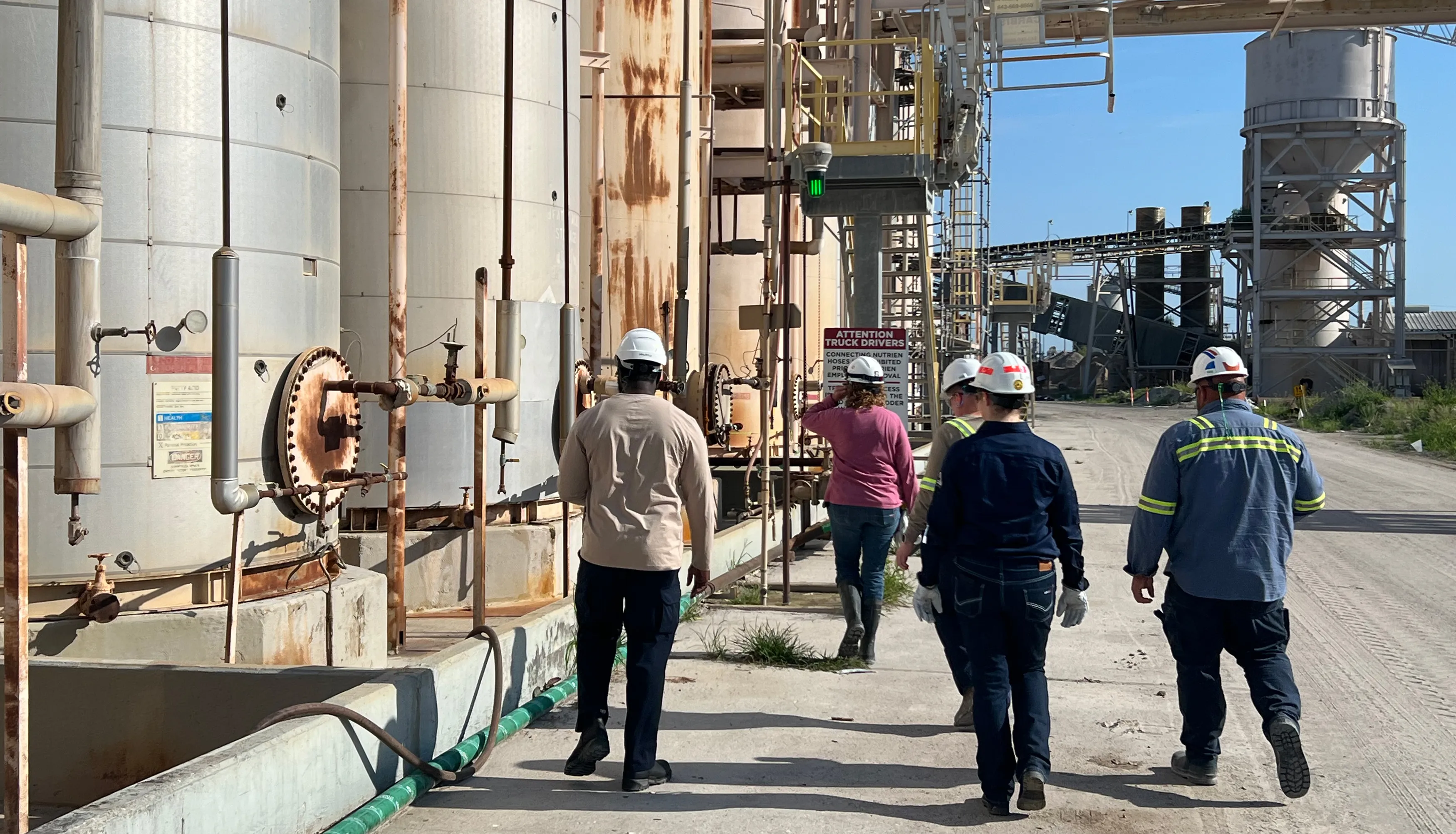