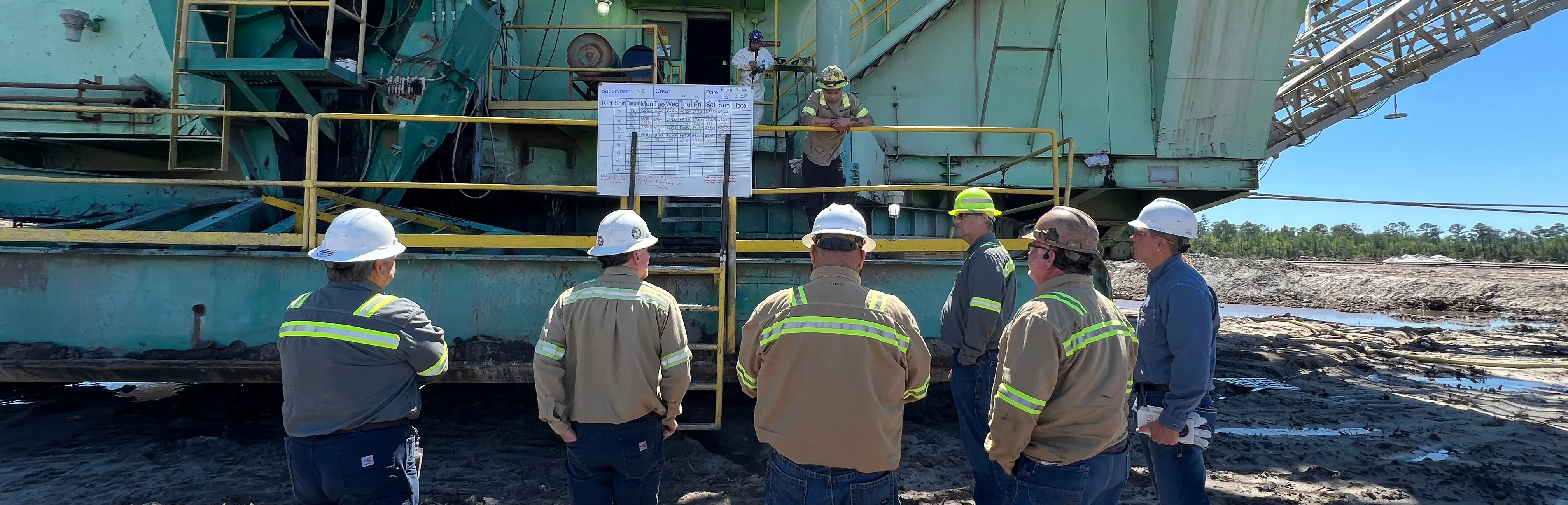
We Bring Expertise Where It Matters
Organizations often fall short of their potential because they are not engaging their front line, aligning stakeholders, and building accountability for strong performance.
Our coaches bring expertise where it matters most, your front line. It is there where better ideas exist, work is done and value is created. By working closely with your teams, we build alignment and accountability, accelerating achievement of your key objectives. Our expertise connects hearts and minds, building internal capability for sustained performance.
We bring industry expertise, effective tools and coaching to co-develop and implement strategies and tactics for improved results, stronger leaders, and engaged employees.
While each customer faces unique challenges, the universal need is to connect the front line to the bottom line in daily ways of working.
Industries We Serve
Our Core Capabilities
Our clients place their trust in our six core capabilities because it enables them to achieve front-line engagement, broader alignment, and wider accountability to achieve operational, project and safety targets.
Where we operate
We have extensive experience working in over 55+ countries. In each country, we leverage our vast expertise and capabilities to navigate the cultural and logistical intricacies of client engagements. For business inquiries, please contact our regional leads.
- Canada: Andrew Zakaluzny
- USA: Michael Doherty
- Europe: Scott McKenzie
- Middle East: Neil Longson
- Asia: Rob Gulbronson
- Australia: Aaron RIcher

Success Stories: Real-World Impact
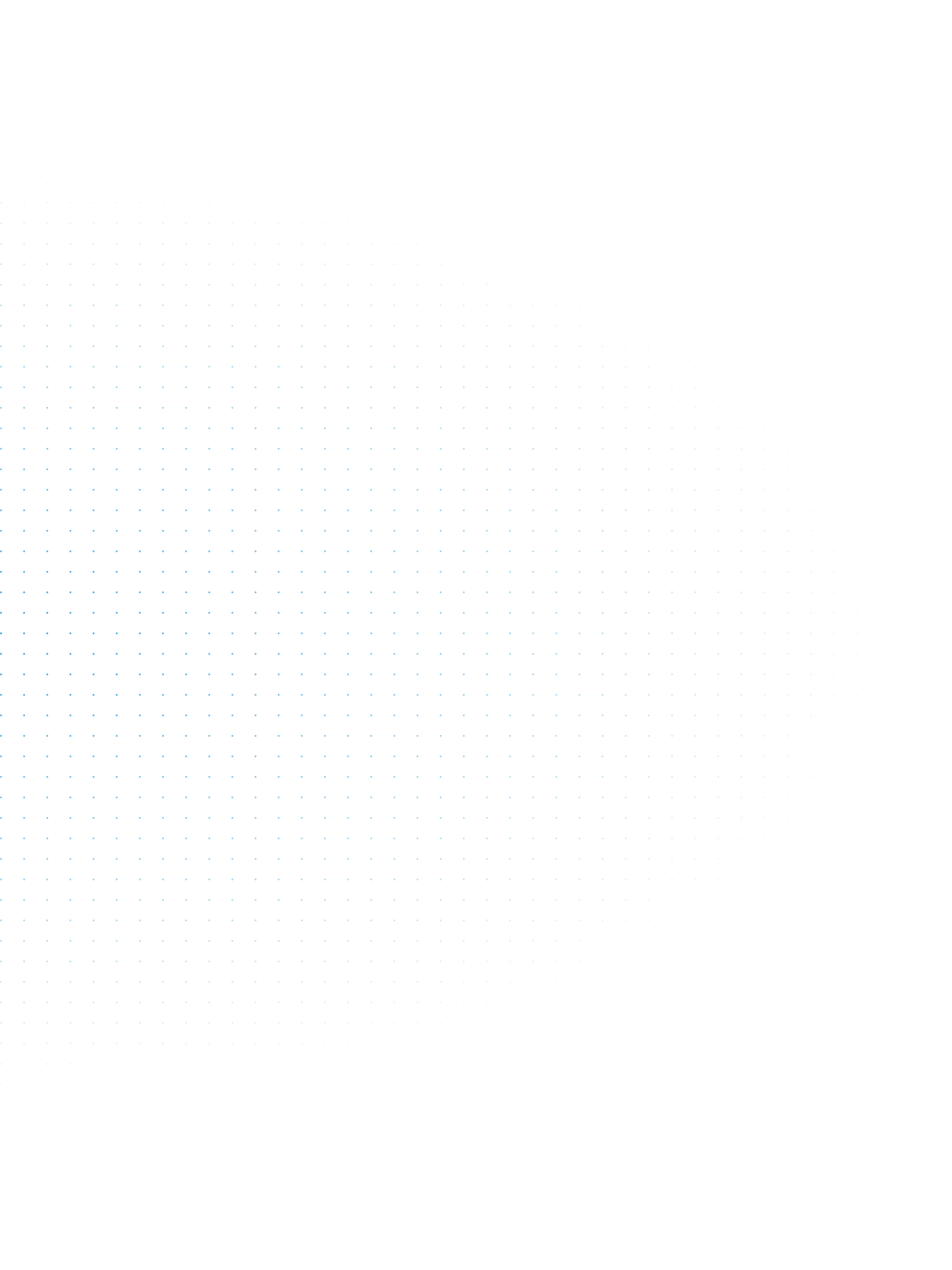
We're hiring!
Our team is growing fast and we can't wait to receive your application!
